Featured
Ole Miss Alumni Review: Maker's Mark
This story was reprinted with permission of the Ole Miss Alumni Review. Spring 2014 Edition
Not so long ago, engineers’ use of three-dimensional modeling software to render an object viewable on a computer screen was considered novel and exciting. Today, the computer rendering is becoming fully realized as it is now possible, and increasingly commonplace, to create individual 3-D objects with the advent of 3-D printing.
At the Haley Barbour Center for Manufacturing Excellence, on the University of Mississippi’s Oxford campus, students now have the opportunity to use this exciting new technology for themselves.
The CME was founded in 2010 and combines the disciplines of engineering, business and accounting to prepare students for careers in manufacturing. The center boasts a fully functional factory floor replica, where students can acquire hands-on experience in a factory setting.
Students in the schools of Business Administration and Accountancy can obtain a minor in manufacturing through the center, and School of Engineering majors can earn an emphasis in manufacturing.

Photo by Robert Jordan
A computer-aided design (CAD) modeling course is a requirement for CME students, and now those students are able to see the physical manifestation of objects they dream up and view on the two-dimensional space of a computer monitor. That simple task is a great learning tool, helping to foster creativity and prepare students for the emerging marketplace.
“It could be something just to visualize the part and then be hands-on and touch it,” says Ellen Lackey (BE 90, MS 92, PhD 96), professor of mechanical engineering and director of composite materials research group test facilities. “Or it could be something useable. Most recently, I had a student print a mouthpiece for a trombone.
“[The course] is for the CME students who are engineering majors, and it’s required,” Lackey says. “But there’s another mechanical engineering CAD modeling course that is a technical elective course that any engineering student can take.”
The technology is moving fast. Six years ago, the center purchased a printer inscribed with a serial number of “2,” meaning it was only the second one made.
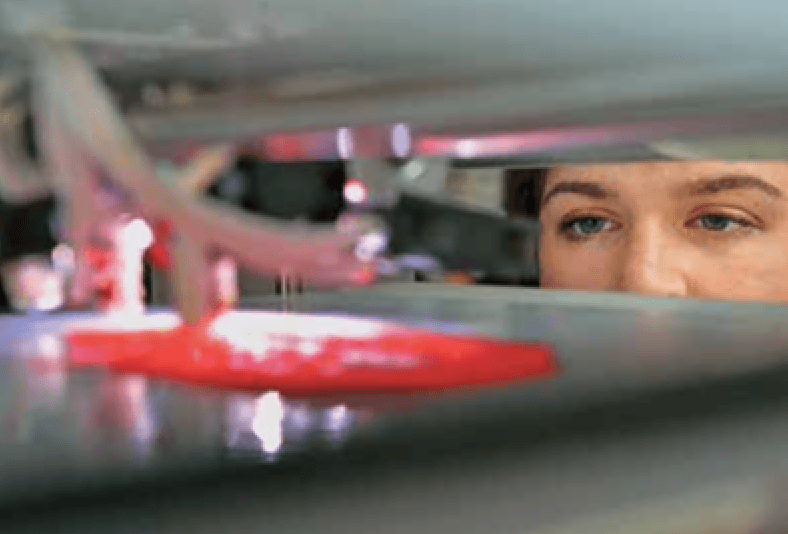
Photo by Robert Jordan
“That one has a pool of liquid. You shine a layer on it; it cures with the light,” says Jimmy Palmer (BSCS 02, MSESC 05), information technology coordinator for the CME. “You shine the next layer, it drops down, then it rises up out of the bath. It’s ABS plastic — very hard, rigid plastic.”
That machine is currently in need of maintenance, the cost of which would equal the cost of a brand new desktop printer such as the one most recently purchased and in use by Lackey’s students.
The newest machine works by taking the computer model and pouring a small tendril of heated plastic in the shape designed by the model. Then it follows with another layer, another and yet another until the object is complete. Depending on the resolution (a higher resolution prints the objects with more and smaller tendrils), an object can be produced in a matter of hours.
“Just like with any other printer that has various resolutions, the higher [the] resolution you print at, the longer it takes to print,” Palmer says. “It depends on how thin the layer is. The thinner the layer, the better the quality is.”
3-D Advantages
Today, the implications of on-demand manufacturing in a desktop setting are far-reaching. Applications in health care, manufacturing, research and development, and military arenas are all in the works. 3-D printing has been used to create props for blockbuster movies. It’s even been used to create food products.
CME students use the printers to help them hone their 3-D modeling skills. Whereas previously they could only look at a 2-D print of their creations and rely on their imaginations to learn what any particular widget they designed would look and
feel like, now they can design it, print it and, in a matter of hours, hold it in their hands.
“The students can now build prototypes of their designs that they created with CAD software,” Lackey says. “That’s beneficial.”
“It’s one thing for a student to take and generate something in a 3-D CAD program like Pro-E or TurboCAD,” Palmer says. “It’s quite another to physically see that. Historically what happened was if they wanted a physical representation, they would’ve had to take raw stock down to the floor, machine it out by hand, or put it on the CAD machine and do it that way. Here they can tell it to print, let it run overnight, and come back in the morning and it’s done.”
In the workplace, 3-D printing has clear advantages.
“Prototyping is the big thing,” Lackey says. “Does the customer like the appearance, the look and feel of [a product]? Does it fit? Some of them, depending on the application, are strong enough to test. Some of the metal printers … you [can] manufacture with it. It might be small-scale manufacturing, but it is manufacturing.”
It’s a timesaver too.
“There are some engineering firms that are making pieces for internal and external clients, and one engineer in his office will have four of these printers,” Palmer says.
“That increases his productivity many times. Normally the way that would [work] is
[the engineers] would design the piece, model the piece, make sure that it works in their virtual design. Then they would have to send it to the factory floor, to the technicians to actually manufacture it, and they might have to wait a week. They may spend [$10,000] or $15,000 a piece on the printers. But in the amount of time it takes five or six people to manufacture that one part, they save money in normally the first year.”
The technology isn’t new but is progressing fast enough that the cost is decreasing to make it feasible for students and small firms to use it. Home models are even coming out now that cost barely more than $1,000.
“3-D prototyping has been available for well over 20 years,” says Lackey. “It was commercial and very expensive. But getting it to the consumer prices – it’s been the past year or so.”
Part of the surging interest and use of the technology is due to other reasons.
“In 2014, a lot of patents are running out,” Palmer says. “A lot of companies are able to get in now because they don’t have to buy the patents. They’re starting to run out from 20 years ago. There’s been a lot of industry consolidation too.”

Photo by Robert Jordan
The machines are helping students to be more creative as well as keep up with technology trends.
“Allowing them to be creative, be able to create something that they can think about is the biggest advantage,” says Jim Vaughan, interim director of the Center for Manufacturing
Excellence. “They can turn their thoughts into an actual 3-D object. They can do it on a computer, and that’s all well and good, but then they can take that to the next step and actually create the object.”
Timothy Steenwyk, a freshman mechanical engineering major with an emphasis in manufacturing, took Lackey’s class and was soon producing his own objects. His first attempt, a heart-shaped keychain he made as a Valentine’s Day gift, required several attempts.
“I think the best way to learn 3-D printing is to just interact with it,” he says. “The way we imagine something is much different [from] the reality.”
Steenwyk says that holding a solid object also gives him a good idea of its scale.
“You can manipulate it with your hands, and you can see if it’s going to work. You get a good estimation. Before, you’d have to know how to input to view things and manipulate it. But in real life, with your hands, it’s just natural. You have a solid prototype in front of you. You already know how to handle objects.”
Innovative Applications
Injecting more creativity in the engineering sector is drawing more people into it. Artists
are using 3-D printers to render sculptures. The worlds of graphic design and engineering
are colliding in ways that before now were unimaginable.
For the blockbuster movie “Iron Man” and its sequels, prop masters simply printed objects such as weapons and parts of the Iron Man costume rather than individually sculpt them.
The gee-whiz, cool-gadget factor of the technology is drawing more students into engineering. A few years ago, the CME conducted a series of camps for high school students. Seeing that technology at work, many of them steered their career planning toward engineering and manufacturing.
“That was the idea behind the summer camp – to show them the cool technology and encourage them to go into areas of STEM and engineering,” Lackey says. “It’s pretty common these days, but it’s still kind of a wow factor. We were doing summer camps before the CME started. We were exposing high school and junior high kids to 3-D printing, and that was six years ago. Nobody had ever seen anything like it, and now people are reading about it in popular magazines.”
As for potential uses of 3-D printing in the workplace, the military is using 3-D printing in the field to replace machinery and parts on the fly. GPS sensors, drone equipment and other technical equipment can now be replaced in the field in a matter of hours instead of days or weeks. And older, outdated equipment that previously was unable to be reconditioned due to infeasibility can now be updated, thanks to 3-D printing.
“I read about an old military plane they couldn’t get any parts for, and now they were able to just manufacture it,” Lackey says.
One of the most exciting areas is in the health care industry. Scientists and doctors have already used 3-D printing to make artificial organs. Prosthetics is also a growing field for 3-D printing. In an industry that relies on individual fit more than perhaps any other, tailor-made limbs are now obtainable.
“Right now, we have straight-to-consumer prosthetics,” Palmer says. “Used to, it would take months and months to get correctly. Now you can print your own, and as you grow, you just print bigger ones. It’s essentially an overnight process. They scan where it’s going to attach the piece exactly the size you need it. Yes, it’s expensive to print, but it is still cheaper than the alternative. You’re going to see this proliferate.”
The “scanning” that Palmer speaks of is the true horizon of the technology. In addition to being able to print a 3-D object, technology is emerging that will allow for objects to be scanned by a 3-D scanner, then rendered into the modeling software and printed as an exact replica. While this development will undoubtedly present a myriad of legal issues concerning copyright, the ability to physically replicate an object on a desktop machine at home seems like something out of “Star Trek,” yet it is already becoming a reality.
As with all emerging technologies, the application ranges from the critically serious to the whimsical. Chocolate 3-D printers are already on the marketplace, with chocolate and
other confectionaries replacing plastics and metals. Crafting food products is constrained only by the imagination of the designer. Following Hewlett-Packard’s naming system
of Inkjets and LaserJets, 3D Systems’ new line of 3-D chocolate printers is called Chefjet.
While sci-fi-sounding as well as mundane applications of 3-D printing are on the horizon, this technology is also a tool to be used now. Teaching Ole Miss students how to use it is not just a novelty; it’s a necessity.
“3-D printing is going to become the new way of making a lot of components in the next few years,” Vaughan says. “The concept of additive printing is going to make a fundamental change to manufacturing. We’re making sure students are aware of its upcoming role in manufacturing and giving them the option to do it and explore
their creative ideas.”
By Tom Speed
Follow HottyToddy.com on Instagram, Twitter and Snapchat @hottytoddynews. Like its Facebook page: If You Love Oxford and Ole Miss…

Ricardo Lane
June 16, 2017 at 7:09 am
Nice Post.